

Because not all asphalt is created the same, engineers need to predict how well an asphalt mixture will perform in addition to the maximum load it can support. While there are many ways of determining this, the Marshall test is one of the most common methods in dictating the best proportion of aggregate and binder materials for a mixed design. By measuring many qualities of asphalt specimen, it progressively narrows in on an optimum asphalt mix design for a specific application.
The Marshall method is a holistic approach to asphalt pavement mix design. Through a series of steps, it is able to establish the ideal asphalt content for a mix that will provide maximum strength and stability for its load. Through Marshall testing, engineers are able to:
- Select mineral aggregate and binder materials
- Measure the strength and flow of materials through load testing
- Test material properties in a lab setting
The Marshall Stability Method was first discovered in 1939 by Bruce Marshall at the Mississippi Highway Department. Due to its simplicity as well as its rapid and effective test results, the method was later adopted by the U.S. Army Corps of Engineers to evaluate asphalt mix designs for World War II airfields. The large military aircrafts required a landing strip able to withstand their extremely heavy loads, something that the Marshall test could ensure. Its popularity spread to many state transportation departments and soon the Marshall test became the most widely used pavement design system in the world.
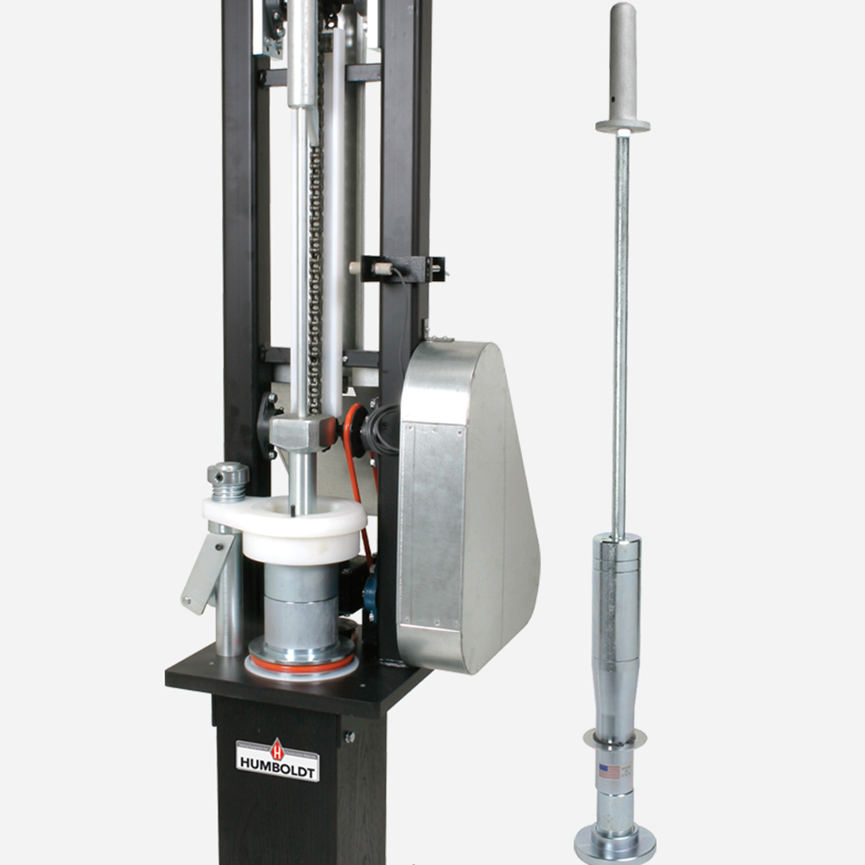
Compaction
Marshall Compactors are used to compact asphalt into molds to prepare specimens for Marshall testing.
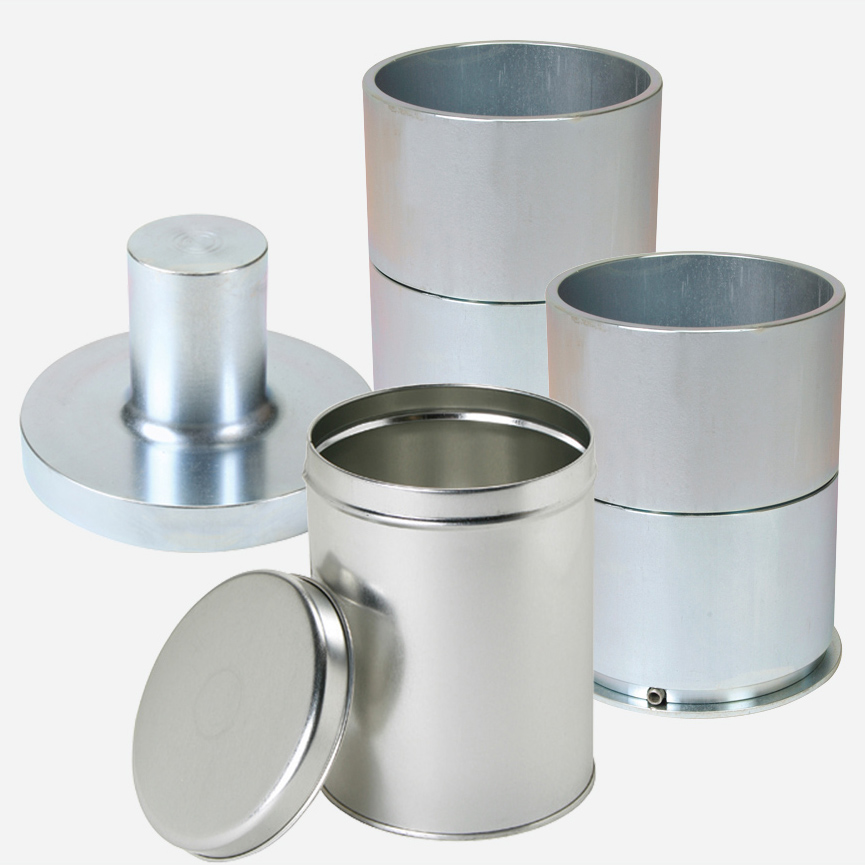
Sample Preparation
The Marshall method uses several trial aggregate-asphalt binder blends each with a different asphalt binder content. By evaluating each trial blend’s performance, an optimum asphalt binder content can be selected.
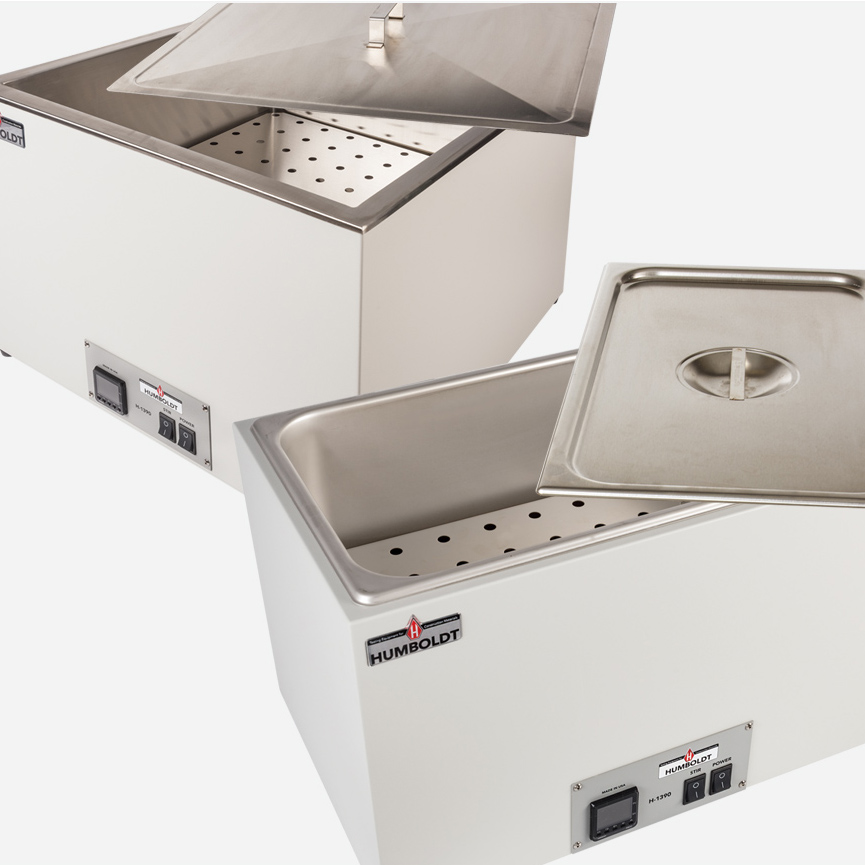
Water Baths
Water Baths allow the samples to be at a controlled temperature throughout the entire Marshall process using heated water to condition the sample.
How to Perform a Marshall Test
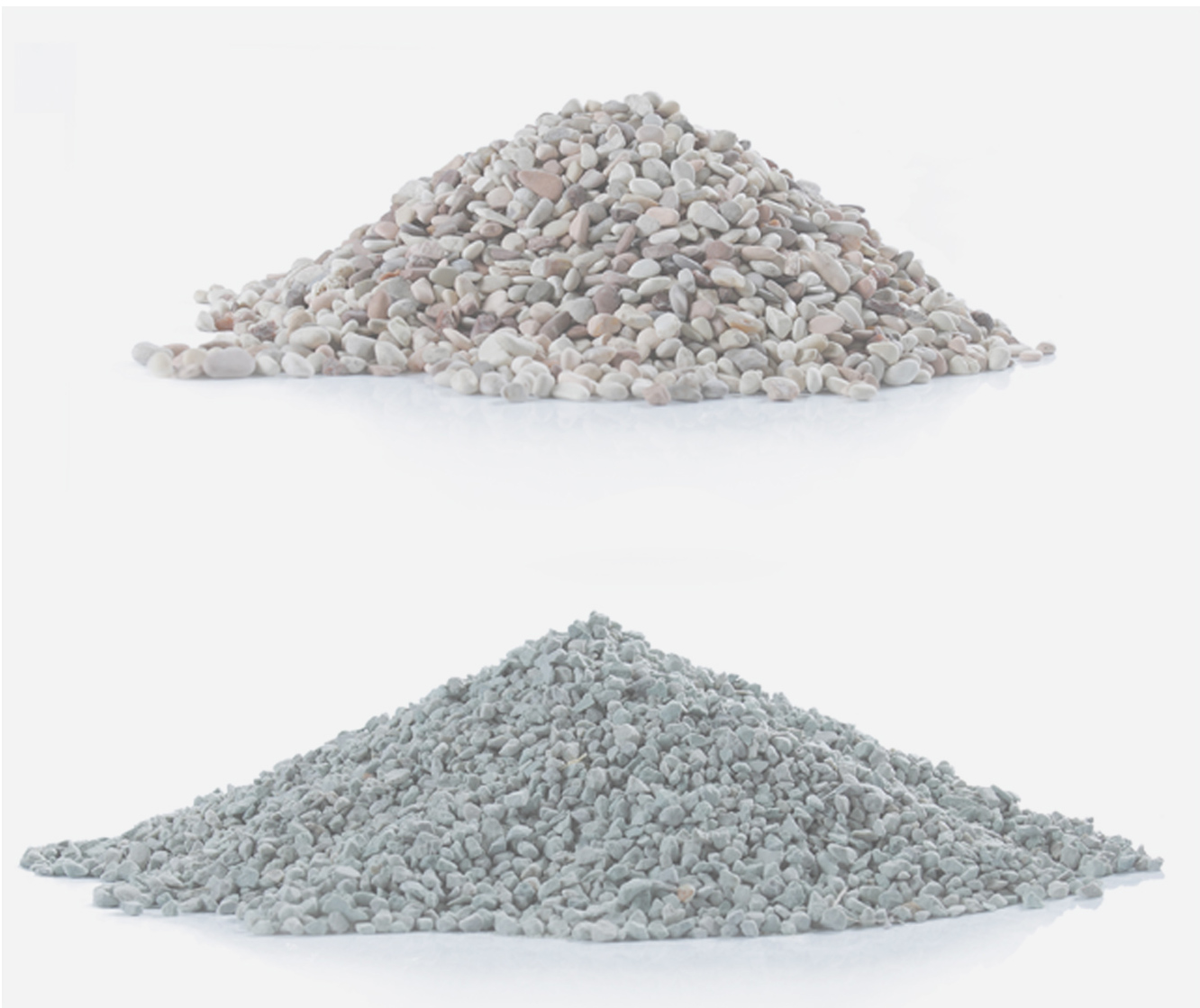
Step 1: Select the Right Aggregate
Asphalt is composed of a mix of aggregates and bitumen to bind them together. Because different asphalts have different purposes, it is important to choose the right aggregate for the job. To select an aggregate, physical properties such as resistance, particle shape, durability and absorption must be carefully tested. Additionally, using more than one type of aggregate for better results requires mix testing during this process. This crucial step ensures strength and stability for the final asphalt mix.
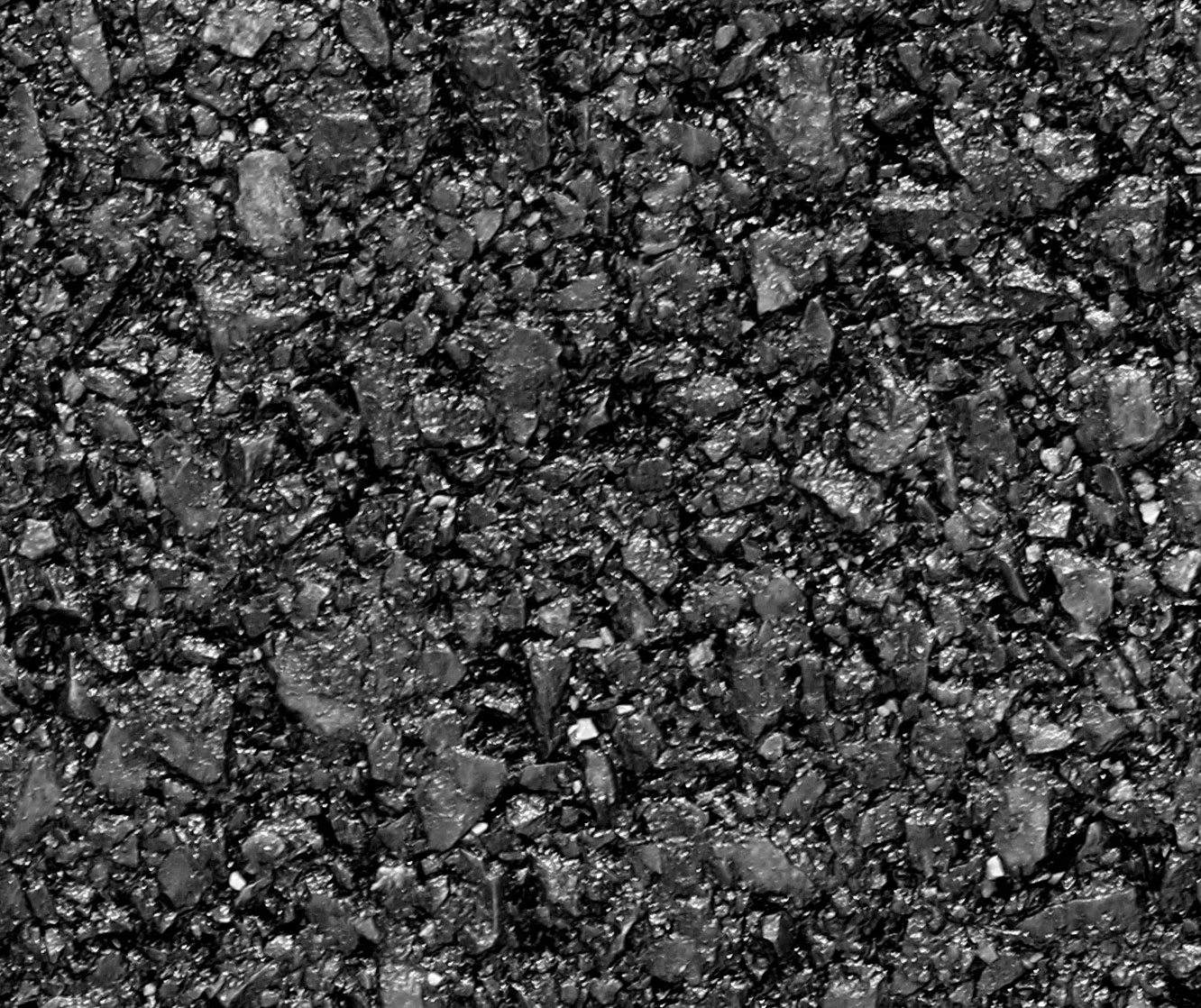
Step 2: Select the Right Asphalt Binder
While the Marshall test has no process for testing binders, this is a crucial action in creating asphalt mixes. While a binder may be chosen based on experience, most commonly, engineers will refer to the Superpave binder system to test the relationship between expected climate conditions and viscosity. This will help to determine which asphalt binder to include in the mix.
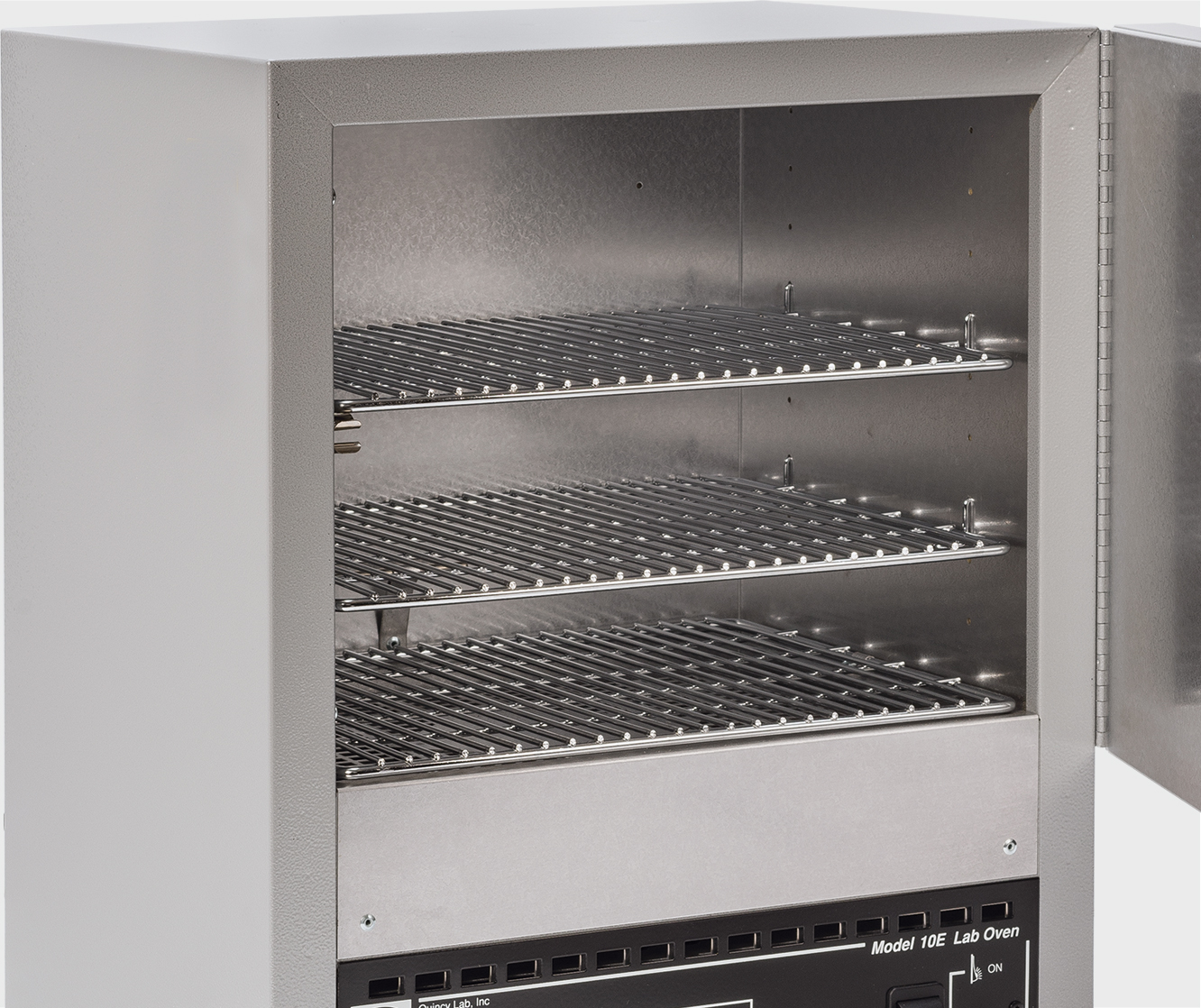
Step 3: Prepare the Sample
In order to choose the best bitumen-aggregate blend for a specific project, many mixtures with varying levels of binder content are tested. Most commonly, 15 samples (five bitumen-aggregate blends with three different levels of binders) are used to determine the optimal asphalt binder content for the application. To further prepare for testing, the 15 samples are heated to the same specific temperature using a lab oven.
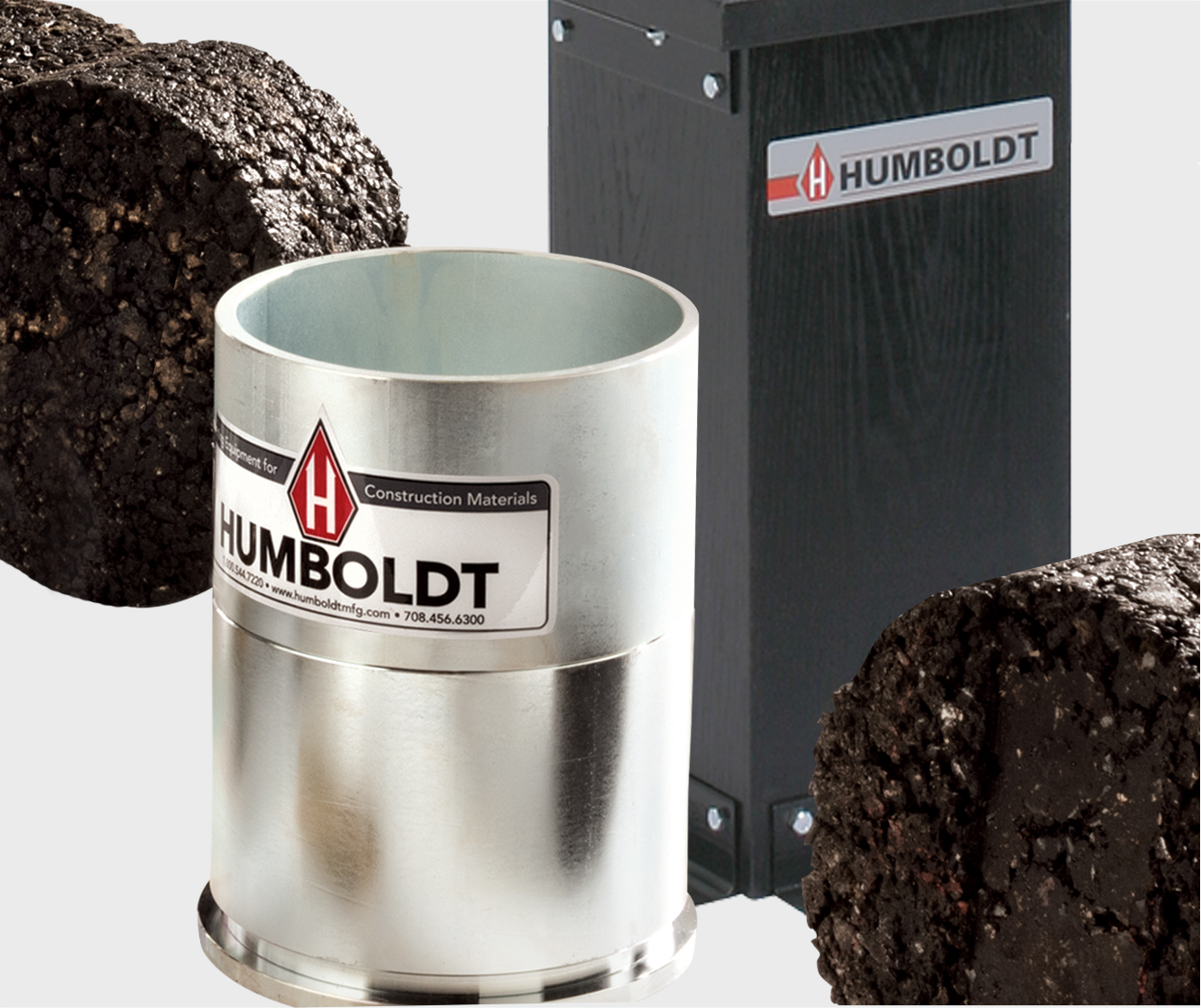
Step 4: Sample Compacting
Once prepared and heated, a Marshall compactor is used to compress the samples with a 10lb steady pressure following ASTM D6926 regulatory standards. The samples are then put into compaction molds of 4” or 6” diameters. Once compacted, the specimens are extracted from the mold using a sample ejector.
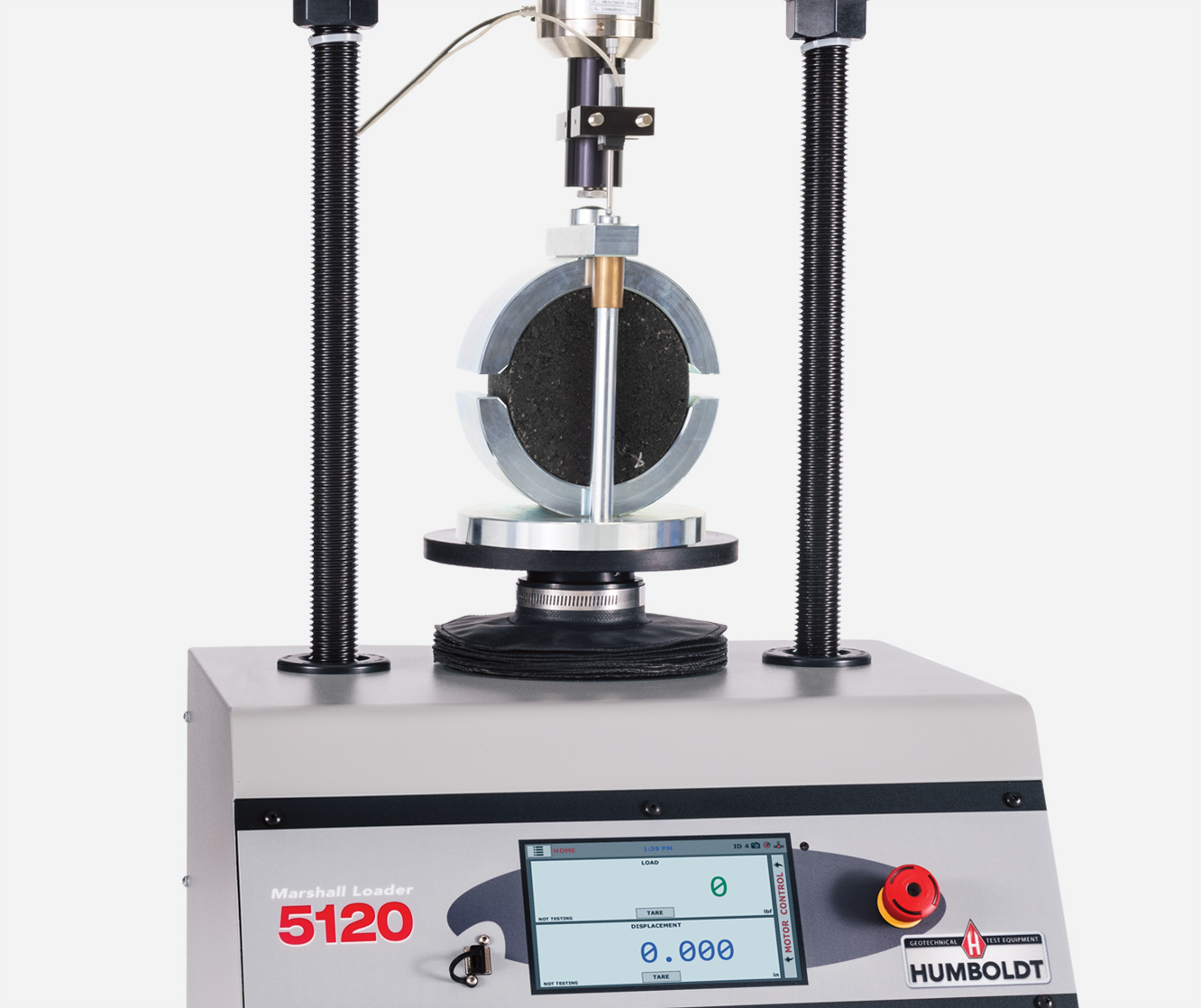
Step 5: Stability and Flow Testing
The next step of the Marshall test is to examine a mix’s stability and flow. The compacted specimens are put into a water bath before being placed into a Marshall breaking head. They are then tested following ASTM D6927 criteria to measure the maximum load a particular blend will be able to support using a Marshall load frame. Loaded at a rate of 2 inches per minute, a sample’s stability is measured as the maximum load it can reach.
During the loading process, a specimen’s plastic flow, also called deformation, is recorded in 0.01 inch increments using a dial gauge. Additional accessories to support the load frame during this step are also available. To make testing quicker and more efficient, Humboldt provides NEXT software that seamlessly connects your equipment to a digital platform. This software is able to record, graph, calculate and report Marshall test values automatically.
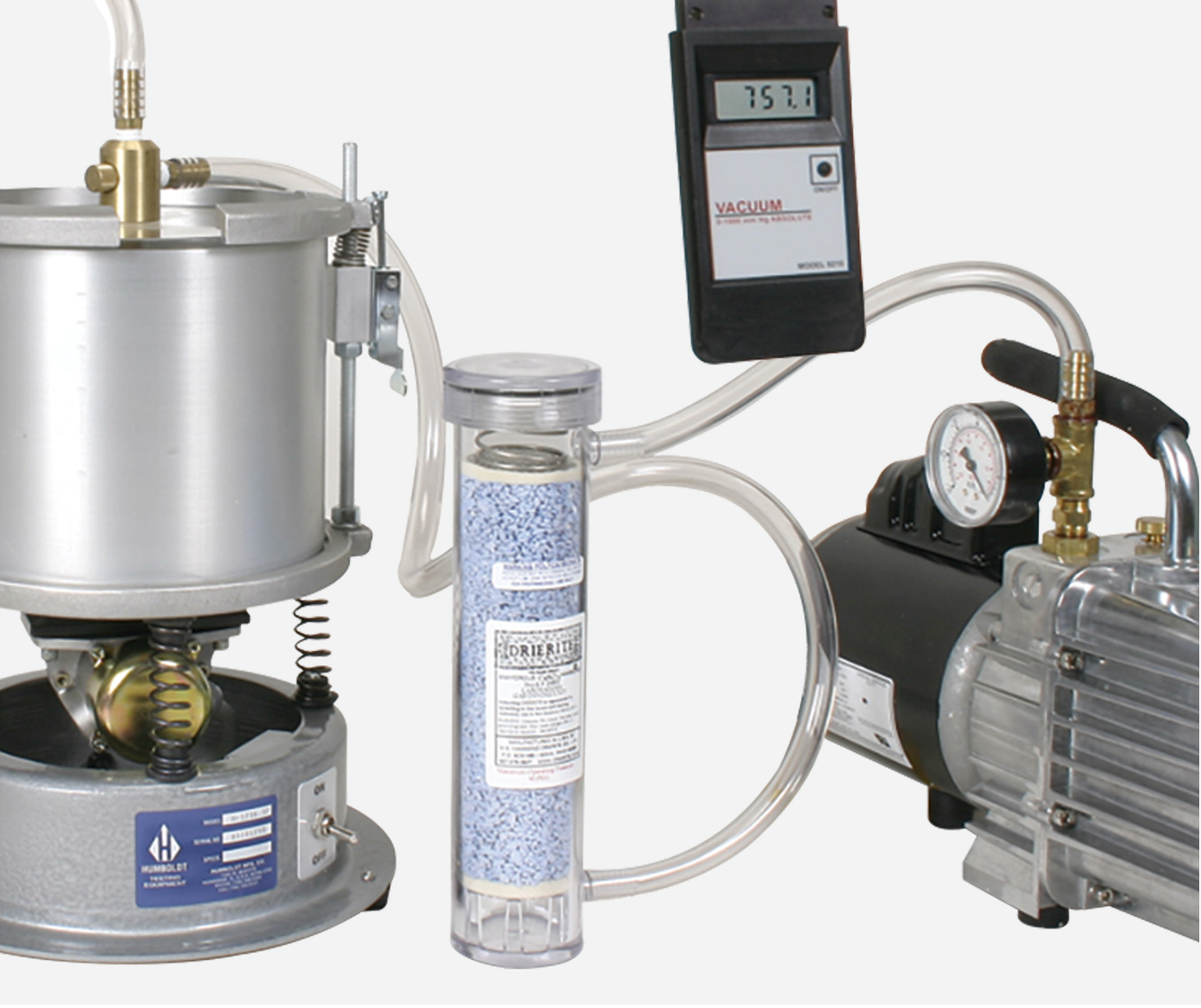
Step 6: Analyze Density and Air Voids
The final step in the Marshall test is to assess the specific gravity and presence of air voids of an asphalt mixture. These tests ensure that the blend meets local and state standards and prevent issues in the future. Specific gravity and density are determined using ASTM D2041 (Rice Test) for loose material and ASTM D2726 for compacted specimen. Air void content on the other hand is tested using ASTM D3203.
Once finished, the Marshall test produces an asphalt mix specific for its intended use. Simple, fast and easy to do, it’s still one of the most popular asphalt tests today. Humboldt supplies the highest-grade Marshall test equipment in many varieties.
If you have questions or need help selecting equipment, please call us at 1.800.544.7220 or use our Ask Humboldt form.